Rework in construction is one of the biggest hidden costs that can throw projects off track, leading to delays, budget overruns, and wasted materials. Studies show that rework can take up as much as 5% of a project’s total cost, with even higher percentages in poorly managed projects.
The good news is that you can reduce rework and keep your projects on schedule with the right approach. In this guide, we’ll break down the main causes of rework and share practical strategies to prevent it. Whether you’re a contractor, project manager, or site supervisor, these proven methods will help you minimize mistakes, improve efficiency, and protect your budget.
What is Rework in Construction?
Rework in construction happens when work needs to be redone or corrected because it was not completed correctly the first time or did not meet project requirements. This can result from design flaws, poor workmanship, miscommunication, or scope changes. Rework leads to wasted materials, higher costs, and project delays, making it a major challenge for contractors and project managers.
How Rework Impacts Construction Projects
Rework can have serious consequences for construction projects, affecting budgets, timelines, and overall efficiency. Here’s how:
- Financial Losses: Every mistake leads to additional labor, material, and equipment costs.
- Project Delays: Fixing errors takes time, often pushing back deadlines and disrupting schedules.
- Lower Productivity: Instead of moving forward with new tasks, workers must redo work, slowing overall progress.
- Client Dissatisfaction: Frequent rework can hurt your reputation and weaken client trust.
The key to reducing rework lies in identifying why it happens and implementing strategies to prevent it before issues arise.
How Much Does Rework Cost in Construction?
The financial impact of rework in construction is significant, reducing project budgets and profit margins. A white paper by ARC Document Solutions, citing industry research, indicates that rework accounts for 5 to 9% of total project costs, with poorly managed projects facing even higher losses. On large-scale builds, this can amount to millions in avoidable expenses.
Beyond direct costs, rework also drastically reduces productivity. Research from nrc-cnrc.gc.ca reveals that rework-related inefficiencies can lead to labor productivity losses of up to 30%, forcing teams to spend time fixing mistakes instead of progressing with new tasks.
The ripple effects do not stop there. Rework disrupts schedules, extends project timelines, and strains relationships between contractors, subcontractors, and clients. In some cases, subcontractors may even walk away from projects due to unexpected delays, causing even more financial strain.
By identifying the root causes of rework and implementing proactive strategies, construction companies can recover substantial cost savings, maintain tighter schedules, and improve overall efficiency, ultimately boosting both their bottom line and reputation.
Common Causes of Rework in Construction
Rework in construction leads to wasted time, materials, and money. While some issues are unavoidable, many can be traced back to preventable mistakes. Here are the main culprits:
Frequent Scope Changes
Last-minute design modifications and unclear project requirements create disruptions. Changes made without proper approval or documentation often result in rework, impacting timelines and budgets.
Poor Planning and Miscommunication
Unclear instructions, lack of coordination, and misaligned expectations often result in costly errors. Without a structured communication process, teams work with conflicting information, leading to mistakes that require correction.
Design Errors and Incomplete Drawings
Flawed blueprints, missing specifications, or outdated plans create confusion on-site. Contractors may follow inaccurate designs, only to realize later that adjustments are needed, leading to delays and added costs.
Inadequate Quality Control
Skipping inspections or failing to enforce quality standards allows defects to go unnoticed until later stages. By the time issues are caught, fixing them becomes more expensive and time-consuming.
Workmanship Issues and Insufficient Training
Inexperienced or poorly trained workers are more likely to make mistakes that compromise quality. Without proper oversight and skill development, these errors become recurring problems.
Best Strategies to Reduce Rework in Construction Projects
Here’s how you can drastically minimize rework and boost efficiency:
1. Leverage Construction Management Software
Platforms like Builtfront help streamline documentation, track progress, and enhance team collaboration. With real-time updates and centralized information, teams can avoid miscommunication and costly errors.
2. Strengthen Team Communication
Clear communication is key to preventing mistakes. Using RFIs ensures project details are properly clarified, while daily site briefings keep teams aligned. Providing real-time updates also helps prevent misunderstandings before they lead to costly rework.
3. Apply Lean Construction Principles
Lean construction eliminates inefficiencies by focusing on better planning and resource management. Standardizing workflows, reducing material waste, and improving coordination between teams all contribute to smoother project execution with fewer mistakes.
4. Enforce Strict Quality Control
- Conduct real-time inspections instead of waiting for final checks.
- Assign dedicated QA teams to monitor each phase.
- Plan tasks in advance to anticipate potential issues.
5. Invest in Workforce Training
A well-trained workforce makes fewer mistakes. Providing continuous education on construction techniques, safety protocols, and quality standards ensures workers have the skills needed to deliver high-quality results.
6. Minimize Last-Minute Scope Changes
Frequent changes create confusion and increase the risk of rework. Setting clear project expectations from the start and enforcing a structured change management process helps keep projects on track. Only necessary modifications should be approved to avoid unnecessary disruptions.
By implementing these strategies, construction teams can significantly reduce rework, keeping projects on schedule and within budget.
How Technology Helps Reduce Rework in Construction
Technology helps construction teams catch mistakes early, improve communication, and keep projects on track. Here’s how:
Building Information Modeling (BIM)
BIM creates a digital version of a project, allowing teams to spot design errors before construction starts. Engineers, architects, and contractors can collaborate better, ensuring everything is accurate and aligned from the beginning.
Drones and AI-Powered Inspections
Drones in construction provide real-time views of construction sites, helping teams catch problems early. AI-powered tools analyze these images to detect errors before they become costly fixes.
Cloud-Based Project Management Tools
Cloud-based software keeps project documents in one place, making it easy for teams to access real-time updates. With everyone working from the same information, miscommunication is reduced, and mistakes are less likely to happen.
Using these technologies makes construction projects more efficient, reduces wasted time and materials, and helps prevent costly rework.
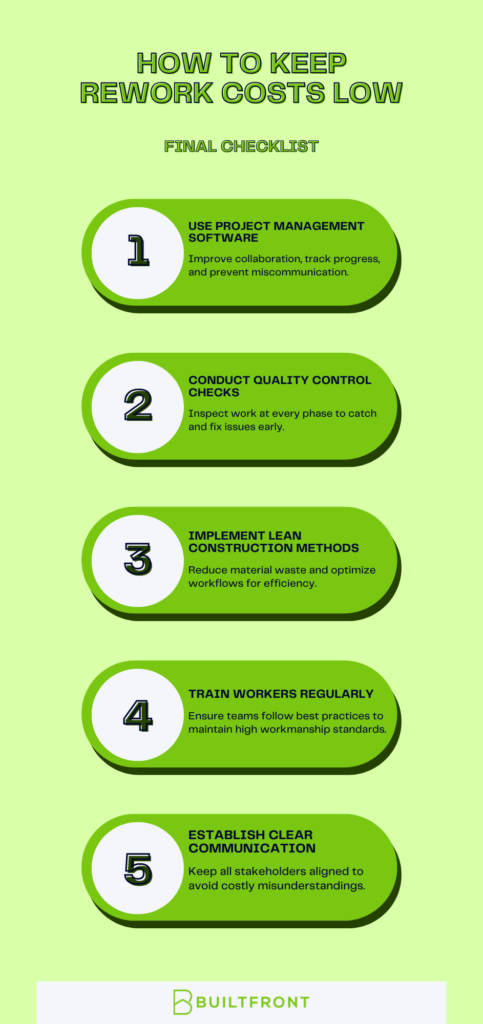
An Easier Way to Reduce Rework
Rework drains time, money, and resources, but most of it can be avoided. With better planning, clear communication, and the right technology, construction teams can reduce mistakes and keep projects on schedule. A strong focus on quality and coordination leads to fewer delays and greater efficiency.
Want to take control of your projects and minimize costly errors? Builtfront gives you the tools to stay organized and prevent rework before it happens.
Ready to build smarter? Start Your Free Trial Now!